A new catalyst has been developed that will enable more environmentally friendly production of plastics and fabrics, claim UCL chemical engineers.
Dr Michail Stamatakis believes that with the difficult part of the development process completed, the new catalyst could be integrated into chemical plants manufacturing propylene, an industry worth 200 billion dollars a year, with 100 million tons of the compound consumed every year in the production of everyday use plastics.
The catalyst was developed with chemical modelling performed by supercomputers, which Stamatakis hopes to use to explore similar developments in the future.
He said: “The prediction ran counter to common wisdom but nevertheless turned out to be incredibly successful when put into practice.”
What is a catalyst?
Catalysts are compounds that change how a chemical reaction works, allowing it to happen faster, at lower temperatures, or with higher purity in the products.
The catalyst isn’t consumed in the process, meaning that a good catalyst can be used for years on end before needing to be replaced.
The process of finding catalysts often involves years of trial and error, allowing the discovery of especially useful catalysts to earn a Nobel Prize in chemistry.
Dr Stamatakis explained that his team were able circumvent the traditional years of trial and error using computer simulations to model large numbers of potential catalysts and identify one which works perfectly.
The catalyst that is used here is made of rhodium, a platinum-like metal worth more than $20,000 for an ounce.
To reduce the extreme cost of using this very rare metal, singular atoms are embedded in a copper sheet, creating an efficient catalyst for a fraction of the cost.
The catalysts created with this method have also proven more resistant to damage, as pure catalysts lose effect over time due to their surface becoming covered in pollutants.
Three years ago the team found a similar catalyst that used platinum atoms in a copper sheet to convert methane into more useful fuels, as methane gas is 25 times more potent than carbon dioxide as a greenhouse gas.
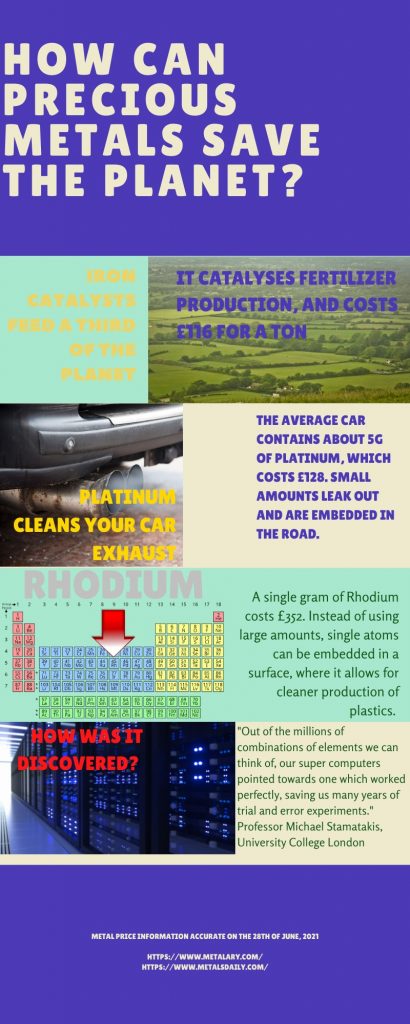
What does this mean for the environment?
Dr Stamatakis explained that the new catalyst allows for a much more efficient production process, that will produce much less pollution.
He said: “The current industrial process that produces propylene releases millions of tons of CO2 as a by-product, whereas our new catalyst is 100% selective to propylene.”
The most prevalent method of manufacturing propylene is steam cracking, which breaks down propane gas into a mixture of different chemicals, only some of which are useful.
Chemical engineers at UCL are looking at other ways catalysis can help the environment without requiring us to consume less.
Dr Stamatakis points to the work in producing catalysts that allow for the efficient breakdown of plastics to enable more efficient recycling.
Similar to the original production process, recycling plastic requires a lot of heat and energy, but they are hoping to reduce the amount required.